For BOBST, its commitment to improvement in productivity and accuracy post-overhauling was the key aspect. As part of its productivity improvement programme, Bobst India recently refurbished two old SPanthera machines installed at Parksons Packaging. Both SPanthera 106 LE die-cutters are housed at its Chakan (Pune) plant. The machines were commissioned in 2007.
Every plant at Parksons sets its targets for OEE increment. OEE has various parameters, such as machine, tooling, logistics, operator skills and more. Parksons checks these parameters regularly, and the two die-cutting machines were required to improve OEE. The company wanted the SPanthera machines to have a high OEE and discussed the project with the Bobst team.
The senior management of both the companies discussed and agreed on this and the project was kickstarted. After the refurbishment, the productivity of the machines has increased by approximately 30%, and registration and embossing accuracy increased substantially. Now, most major electronic/electrical components have obsolescence protection for the next few years.
The process
The first step was to thoroughly inspect the machines under the Bobst Maintenance Plus programme. Then came the replacing of worn out and obsolete parts with new ones, restoring various machine settings, and finally testing the overhauled machines with key jobs for productivity and registration accuracy.
The efforts resulted in two transformed machines with increased productivity, accuracy and availability. The Parksons team expects that the increased production capacity of these SPanthera machines will give a boost to its overall plant OEE. The machines, which were running at around 5,000 to 5,500-sheets/hr, are now able to run at 8,000 to 9,000-sheets/hr.
The Parksons team can also achieve consistent registration accuracy on fine micro embossing jobs, which was a concern previously. The machines are consistently performing well after being refurbished.
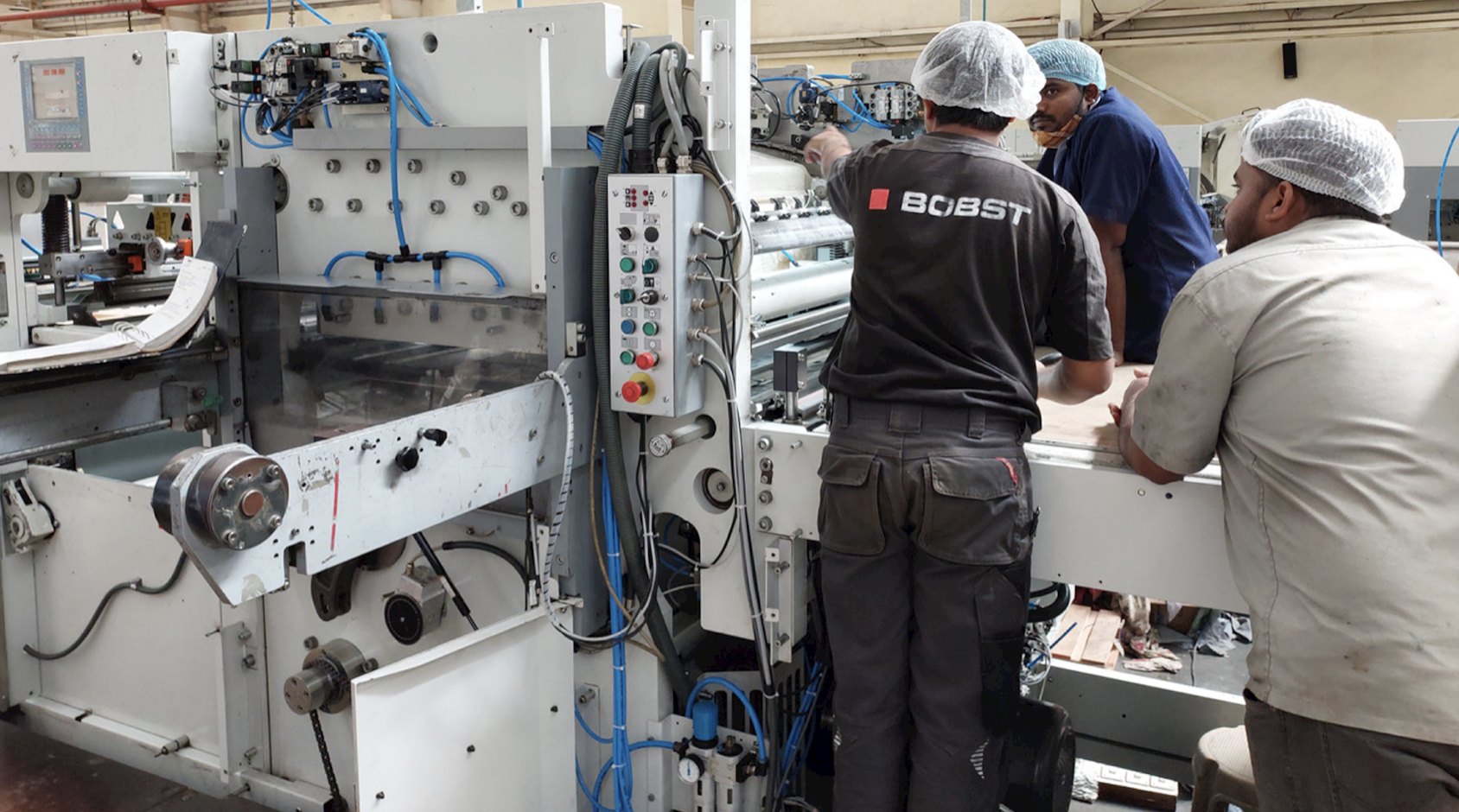
The partnership
Senior service engineers from Bobst, Vikas Kumbhar and Saran Kumar, as well as technical service manager, Vasant Hasabnis, said, “We were thrilled to be involved in the execution of this one-of-its-kind project which transformed these two machines. This experience has given us the confidence to do more similar projects successfully.”
Sameer Joshi, zone services director at Bobst India said, “We appreciate and thank the Parksons management and the Pune plant team for the willingness shown to transform these two machines through a collaborative effort, which was supported by the Bobst headquarters in Switzerland. This transformation can surely be a reference for more such projects in the Indian market.”
Harjit Singh, Maintenance Head, Parksons Packaging, Pune, said, “We are happy with the outcome and have been receiving support from the Bobst team and our feedback is taken seriously. We appreciate the efforts of the team which works collaboratively with us to maintain our machines.”
BOBST Maintenance Plus programme
The Bobst Maintenance Plus programme provides planned, preventive maintenance of Bobst machines, by trained Bobst technicians, using genuine Bobst spare parts. Each enrolled machine undergoes at least one cycle, comprising a health check-up, corrective actions and settings optimisation each year. This improves the OEE of the machines, which is the biggest benefit to the customers. As an additional benefit, Bobst offers a concessional service rate for machines enrolled under this programme and this rate is applied not only for the planned activities but also to emergency breakdowns (if there are any).