Saica Group, founded in 1943 in a small paper mill in Zaragoza, is one of the leading companies in Europe for sustainable solutions for paper and packaging manufacturing, as well as for waste management and recovery. Saica Pack prides itself on offering end-to-end innovative and cost-effective corrugated packaging solutions to customers in a variety of industries, including food and beverages, health and beauty and many more. Today, Saica Group has more than 10,000 employees across 11 different countries and has annual consolidated sales of over €4.3 bn. Saica Pack operates across 51 sites globally, including nine in the UK and two in Ireland.
“Saica continues to invest heavily in the UK. The most significant example of this commitment to growth has been the new flagship Saica Pack facility that opened during 2023 in Livingston, Scotland,” explains Brian Lister, UK & Ireland Country Manager, Saica Pack. “The project began back in 2020, but due to COVID, took time to formulate. We were proud to open the plant in 2023.”
The total investment into the Livingston facility stands at over £50m, a significant investment that demonstrates Saica’s commitment to the Scottish market for the long-term.
He continues, “A lot of our production is for the FMCG sector, and much of this is in food and drink, so we are an important part of that supply chain. We produce attractive packaging for food, beverages, detergents; as well as many other industries and business sectors from e-commerce to distribution. The strategic investment in the Livingston factory has enabled Saica Pack to further expand our customer base, increasing our capacity and offering for customers in Scotland. A notable success has been the work done for Dewars White Label at the Livingston facility, a successful collaboration that led to two nominations at this year’s FlexoTech Awards.”
State of the Art
“The Livingston manufacturing facility features state-of-the-art technology, and we are really proud of it. A substantial amount of in-depth research was conducted to ensure that the facility would not only meet current client needs but also anticipate future market trends,” continues Lister.
He adds, “A key part of that research was establishing exactly what machinery would be required on site. Notable items of equipment include a Fosber S/Line corrugator, which is a wider corrugator with improved run speed to improve lead times and enable automatic control of running parameters vs board grade. We also have an Avanti conveyor system, which has led to a more efficient operation, an improvement in health and safety, reduced work in progress damage, and maximum converting machine outputs. And we have a range of new BOBST machinery to enable precision printing, cutting, folding and gluing.”
The corrugator is a 2.8m wide S/Line doublewall corrugator producing B, C and P flute combinations. The line features Fosber’s LINK-M3 triple position integrated roll stand and splicer for the fastest roll change cycle times with enhanced automation to reduce wet-end manpower. The Smart 400 single facers allow fast flute change flexibility, while Fosber’s ‘oil-free’ dry-end sports gapless order change at line speed along with automatic cut-to-pattern preprint capability.
The complete line is fitted with Fosber’s bespoke single skin sound enclosure reducing noise levels to below 85dB. The line also sports the full range of Fosber’s Industry 4.0 solutions which includes full Syncro4 process controls, augmented reality production supervision and the Pro/Care intelligent maintenance management complete with advanced on board diagnostics and real-time corrugator consumption monitoring for each board quality produced. The Pro/Quality defect detection system automatically detects, corrects and removes waste from the corrugator.
The factory in Livingston also boasts a pioneering automatic vertical warehouse. The ‘Vertical WIP’, installed by Duro Felguera Logistic Systems and UK agent, Avanti, is the first of its kind in the UK and Ireland corrugated industry, and brings energy efficiency gains, increased safety and fully flexible work in progress storage.
For Avanti, the project was based on how to create a full automated high-volume factory from an existing storage facility. “Working with an existing building layout that had insufficient space for a traditional work in progress flat conveyor layout, we proposed the use of an Automatic Storage and Retrieval System (ASRS) from Duro Felguera,” explains Simon Mander, Managing Director, Avanti. “This enabled large volumes of work in progress to be stored and transformed the existing site into the functionality of a classic greenfield layout. The handling system delivers loads from the Fosber corrugator to the ASRS, then ASRS to each converting machine fully automatically.”
Safety was also paramount in the design criteria. To ensure zero pedestrian access to the transfer car aisles, Avanti supplied their WISDOM – Automatic Waste Ink Stereo Die Automated Delivery System. Once converted, all work flows through the Avanti Double Mainline/Double Centralised Palletising system under RF Control and Tracking. Capable of 220 pallets per hour, with large pallet storage – all under control of the Avanti iMPRESS SCADA system ensures a smooth flow through the factory.
Growing Demand
Lister continues, “The primary driver behind the decision to invest in the new factory in Livingston was the growing demand for high-quality, sustainable packaging solutions across various industries. Changes in customer demand, aging facilities and challenges associated with existing site locations led the company to take a major step to increase Saica Pack’s capacity and offering for its customers.
“Investing in state-of-the-art technology has meant that we can improve our total output, which will in turn put us right at the forefront of the industry. The machinery and processes that have been implemented significantly improve operational efficiency. This not only allows Saica Pack to deliver products more quickly but also enhances quality and precision in the packaging process.”
Lister adds, “Another important aspect of the rationale is our environmental impact. Saica Pack is committed to sustainability, and advanced equipment often comes with features that enable energy efficiency and waste reduction, aligning with the company’s goal of minimising its environmental footprint.”
Industry Leaders
Talking about the machinery chosen, Lister continues, “The new corrugator will enable us to improve our output. The corrugator is wider, 2.8m compared to the 2.1m corrugators at the previous Scotland sites. It also has an improved run speed of 420 m/min.
“The four BOBST flexo converting lines have an array of features that will make the entire production process much more efficient. For example, the multi anilox roll system allows for optimised print coverage and quality for all substrate types. The Duo and Tri Fold technology allows two or three cases to be produced from a single sheet, whilst the four colour rotary die-cutter can be customised, so it has internal and external printing capability in a single machine pass.”
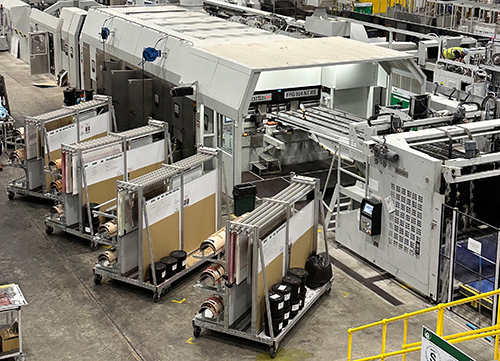
Four jobs staged on bcm tooling trolleys, to ensure ink, stereos and dies are on hand for fast job changes.
Solid Relationships
“Our experience working with the suppliers for installation and training was very positive,” confirms Lister. “From the outset, they demonstrated a high level of professionalism and expertise in their field. The installation process was efficient and well-coordinated. Importantly, this ensured no disruption to our operations. Furthermore, the training provided from all partners was thorough and tailored to our specific needs. As a result, our operators quickly became proficient in running the new machinery. These productive partnerships with the suppliers have been a key factor in the success of the new facility.”
He adds, “Our relationships with the suppliers have been a pivotal factor in the successful launch of this facility. It was, without a doubt, a deeply collaborative effort that brought this vision to life. The relationships that we formed with our suppliers were based on a shared commitment to excellence and a mutual understanding of the project’s significance. This shared commitment was present from the outset and culminated in the successful opening of a site that boasts the latest and most innovative technologies. We look forward to a continued successful collaboration with our suppliers in the future.”
For the Future
Saica Pack also recently invested heavily into its Wigan operation, consolidating two locations into a single site. “Additionally, we have invested in an exciting new B2B App. The app provides a 360º service to customers who can now manage their relationship with Saica quickly, and easily,” concludes Lister. “The packaging sector is an exciting place to be right now, and as a company that is at the forefront of sustainable packaging solutions, I think we’ll continue to see a lot of innovation and investment as companies seek ever-more sustainable supply chains. I am confident we’ll be at the leading edge of this innovation, so watch this space.”